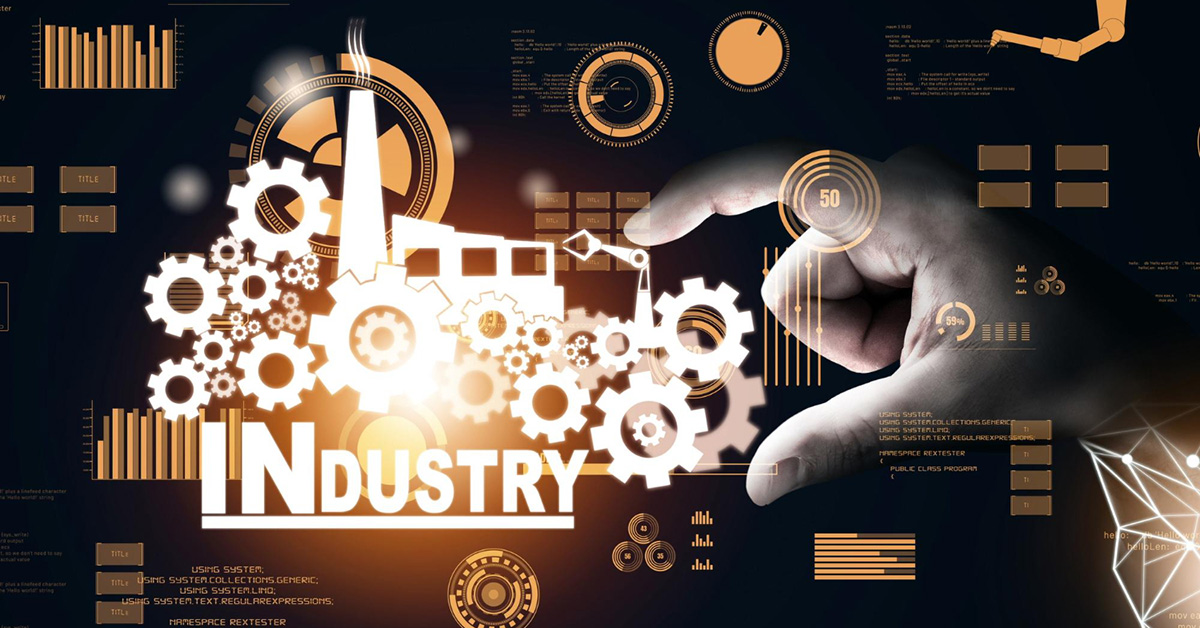
Introduction to Casting Machine Components Manufacturing
In the fast-paced world of manufacturing, every second counts. For a casting machine components manufacturer, efficiency isn’t just a goal; it’s a necessity. With the right strategies in place, companies can not only enhance productivity but also improve quality and reduce waste. The landscape is competitive, and staying ahead requires innovative thinking and smart practices.
As manufacturers seek to optimize their processes, understanding how to maximize production efficiency has become crucial. This article will explore essential tactics that can transform operations at a casting machine components manufacturer into well-oiled machines ready to tackle challenges head-on. Get ready to dive into practical solutions that can take your production game to the next level!
Importance of Production Efficiency in the Manufacturing Industry
Production efficiency is a cornerstone of success in the manufacturing industry. It directly affects profit margins and competitiveness.
When processes run smoothly, resources are utilized effectively. This reduces waste and lowers operational costs. A streamlined operation allows manufacturers to respond quickly to market demands.
Moreover, efficient production enhances product quality. Consistent output leads to fewer defects and higher customer satisfaction. Happy customers translate into repeat business.
In today’s fast-paced environment, staying ahead requires agility. Efficient systems enable companies to pivot swiftly, adapting their offerings as needed.
Additionally, improved efficiency boosts employee morale. When workers see the results of their efforts reflected in productivity gains, it fosters a sense of accomplishment.
Focusing on production efficiency cultivates resilience within an organization. Manufacturers that prioritize this aspect are better equipped for growth and sustainability in an ever-evolving landscape.
Common Challenges Faced by Manufacturers in Maximizing Production Efficiency
Manufacturers often encounter several hurdles when striving for production efficiency. One of the main challenges is equipment maintenance. Downtime can significantly affect output, leading to missed deadlines and increased costs.
Another key issue is workforce management. Finding skilled labor that aligns with productivity goals can be difficult. High turnover rates further complicate this aspect, hindering team cohesion and knowledge retention.
Supply chain disruptions also pose a significant challenge. Fluctuations in raw material availability or delays in delivery can stall production lines, causing inefficiencies.
Additionally, many manufacturers struggle with outdated processes. Legacy systems may not support modern demands, preventing companies from fully optimizing their operations.
Communication gaps between departments can lead to misunderstandings and delays in decision-making—an obstacle on the path to maximizing efficiency across all levels of production.
Strategies for Improving Production Efficiency at a Casting Machine Components Manufacturer
Improving production efficiency at a casting machine components manufacturer involves several targeted strategies. First, analyzing the workflow can reveal bottlenecks. Streamlining processes ensures that each stage flows smoothly into the next.
Next, embracing advanced machinery can significantly reduce cycle times. Investing in state-of-the-art equipment enhances precision and minimizes waste.
Another effective strategy is optimizing inventory management. Just-in-time systems lower carrying costs while ensuring that materials are available when needed.
Additionally, fostering open communication among teams encourages collaboration and innovation. Regular meetings allow employees to share insights on potential improvements.
Setting clear performance metrics helps track progress over time. Monitoring key performance indicators ensures that goals align with overall productivity targets. These methods collectively create an environment where efficiency thrives.
Utilizing Technology and Automation in the Manufacturing Process
Embracing technology and automation can significantly enhance production efficiency. Advanced machinery, such as CNC machines and robotic arms, streamline complex tasks. They ensure precision while reducing human error.
Implementing software solutions for inventory management also plays a crucial role. These systems provide real-time data analysis, enabling prompt decision-making. When you know exactly what materials are on hand, it minimizes delays in the production line.
Furthermore, using IoT devices allows manufacturers to monitor equipment performance continuously. Predictive maintenance becomes possible through data collected from these devices, reducing downtime caused by unexpected failures.
Integrating machine learning algorithms helps optimize workflows too. By analyzing historical production data, manufacturers can identify bottlenecks and implement corrective actions swiftly.
Incorporating these technological advancements transforms traditional manufacturing processes into agile systems capable of responding to market demands efficiently.
Implementing Lean Manufacturing Principles
Implementing lean manufacturing principles can transform the way a casting machine components manufacturer operates. The focus is on minimizing waste while maximizing productivity. This approach streamlines processes, ensuring that every step adds value to the final product.
Start by identifying areas of inefficiency within your production line. Tools like Value Stream Mapping are invaluable for pinpointing bottlenecks and redundant steps. Once these have been identified, take action to eliminate them.
Empowering employees plays a crucial role in this transformation. Encourage team members to contribute ideas for improvement and hold regular brainstorming sessions. Their insights often lead to innovative solutions that boost efficiency.
Regularly review performance metrics as well. Tracking progress keeps everyone aligned with goals and highlights areas needing attention or adjustment. Lean isn’t just a one-time effort; it’s an ongoing commitment to excellence in manufacturing practices.
Employee Training and Continuous Improvement Initiatives
Employee training is vital in maximizing production efficiency at a casting machine components manufacturer. When workers are well-versed in their roles, they perform tasks with greater precision and speed.
Continuous improvement initiatives foster a culture where employees feel empowered to share ideas. This leads to innovative solutions that can streamline processes and reduce waste.
Regular training sessions keep the team updated on new technologies and methods. It also enhances safety practices, minimizing workplace accidents that could disrupt production schedules.
Encouraging feedback loops between management and staff creates an environment of collaboration. Employees become more engaged when they see their suggestions implemented, driving further improvements.
Investing in employee development not only boosts morale but also contributes significantly to operational success. A skilled workforce adapts quickly to changes, ensuring the manufacturing process remains efficient amid industry shifts.
Cost-Effective Sourcing and Supply Chain Management
Cost-effective sourcing is a critical component of maximizing production efficiency at a casting machine components manufacturer. By identifying reliable suppliers who offer quality materials at competitive prices, manufacturers can significantly reduce expenses.
Building strong relationships with multiple vendors allows for better negotiation opportunities. When supply chain disruptions occur, having alternative options ensures that production continues smoothly without costly delays.
Adopting just-in-time inventory practices minimizes holding costs and reduces waste. This approach encourages collaboration across the supply chain, leading to improved communication and timely deliveries.
Leveraging technology also plays a vital role in optimizing sourcing decisions. Data analytics can provide insights into market trends and supplier performance, enabling informed choices that align with operational goals.
Investing time in thorough research guarantees that manufacturers secure the best value while maintaining high standards for their products. Implementing these strategies will not only enhance profitability but also strengthen overall competitiveness in the industry.
Case Studies: Successful Implementation of Production Efficiency Strategies
Examining real-life examples can provide valuable insights into the strategies that lead to significant improvements in production efficiency. Various casting machine components manufacturers have successfully implemented innovative approaches, transforming their operations and outcomes.
One notable case involves a manufacturer that integrated advanced automation technologies into its production line. By employing robotic systems for material handling and precision machining, they reduced cycle times by 30%. This not only boosted output but also minimized human error, leading to higher product quality.
Another example showcases a company embracing lean manufacturing principles. They conducted value stream mapping sessions to identify bottlenecks in their processes. Streamlining workflows resulted in a remarkable 25% reduction in waste, allowing them to allocate resources more effectively and increase overall productivity.
A third case highlights the importance of employee training programs focused on continuous improvement initiatives. A firm invested heavily in upskilling its workforce through workshops on best practices and new technologies. As employees became more adept at identifying inefficiencies, they contributed ideas that further optimized processes—resulting in an impressive uptick in operational performance.
These success stories illustrate how diverse strategies can work together harmoniously within different organizations. Each approach tailored uniquely to specific challenges demonstrates the potential for achieving remarkable gains when prioritizing production efficiency at a casting machine components manufacturer. The lessons learned from these implementations serve as inspiration for others looking to enhance their own manufacturing capabilities while remaining competitive within the industry landscape.