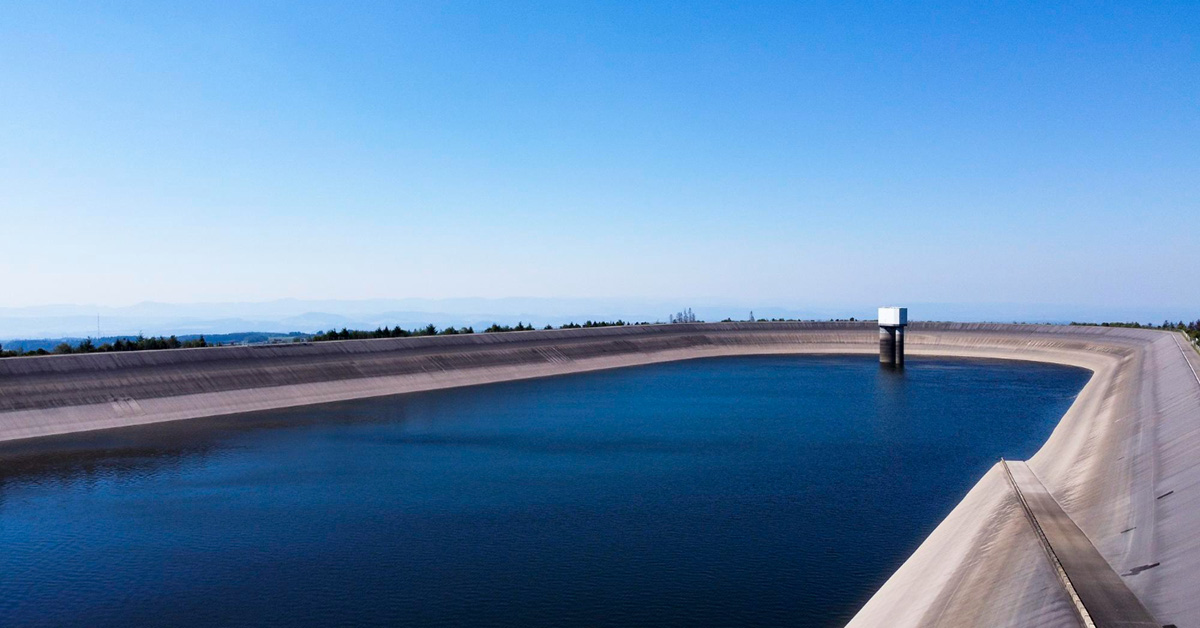
Introduction to Plastic Extrusions
When it comes to creating long-lasting indicators, the materials you choose can make all the difference. If you’re seeking durability and versatility, plastic extrusions might just be your answer. These innovative products offer a world of possibilities that extend beyond standard applications. With their unique properties and customization options, they are quickly becoming the go-to choice for various industries. Let’s explore why plastic extrusions are not only practical but also an investment in quality and longevity. Whether you’re working on signage, framing, or any other project requiring reliable markers, understanding the advantages of plastic extrusions is essential for making informed decisions that stand the test of time.
Benefits of Using Plastic Extrusions
Plastic extrusions offer numerous advantages that enhance their appeal across various industries. One of the primary benefits is their ability to create complex shapes and profiles with precision. This flexibility allows manufacturers to design components tailored to specific needs.
Another notable advantage is weight reduction compared to traditional materials like metal. Lighter products can lead to lower shipping costs and easier handling during installation or assembly.
Additionally, plastic extrusions are resistant to corrosion and chemicals, making them ideal for harsh environments. They require minimal maintenance, which saves time and resources in long-term applications.
Moreover, the manufacturing process itself is efficient. Extrusion techniques allow for rapid production runs, ensuring quick turnaround times without compromising quality. This speed can significantly impact project timelines positively.
Plastic extrusions are recyclable, contributing to sustainability efforts while maintaining performance standards throughout their lifecycle.
Versatility and Customization Options
Plastic extrusions shine with their remarkable versatility. They can be molded into countless shapes and sizes, making them ideal for a wide range of applications. This adaptability is key in meeting specific project requirements.
Customization options are abundant. From varying colors to unique textures, manufacturers can create tailored solutions that fit any aesthetic or functional need. Whether you require intricate profiles or simple designs, plastic extrusions can meet those demands effortlessly.
The ability to incorporate various materials also enhances customization possibilities. For instance, adding UV stabilizers or flame retardants ensures the product performs well under diverse conditions.
This flexibility allows businesses to innovate freely without being constrained by material limitations. With plastic extrusions, your vision can take shape just as you imagined it—down to every last detail.
Durability and Longevity
When it comes to durability, plastic extrusions shine brightly. They are resistant to various environmental factors such as moisture, UV rays, and chemicals. This resistance ensures they maintain their integrity over time.
The lifespan of these materials is impressive. Many extruded plastics can last for years without significant wear or degradation. This longevity makes them a reliable choice for numerous applications.
Unlike other materials that may corrode or rust, plastic extrusions offer consistent performance under challenging conditions. Whether used in construction or manufacturing processes, their strength remains intact.
This resilience translates into fewer replacements and repairs needed down the line. Businesses benefit from reduced downtime and lower maintenance costs due to the long-lasting nature of these products.
Choosing plastic extrusions means investing in solutions that stand the test of time while delivering robust performance across various sectors.
Cost-Effectiveness
Cost-effectiveness is a key advantage of plastic extrusions. Businesses constantly seek ways to reduce expenses without sacrificing quality.
Plastic materials are generally less expensive than metals or other alternatives. This makes them an attractive option for various industries. When you choose plastic extrusions, you often enjoy lower raw material costs.
Manufacturing processes for plastic extrusions can also be more efficient. They require less energy and time compared to traditional methods, leading to reduced production costs.
Additionally, the lightweight nature of plastic means lower shipping fees and easier handling during installation.
Long-term savings come from reduced maintenance needs as well since plastics resist corrosion and wear better than many other materials.
These factors combined make plastic extrusions a smart financial choice for those seeking durable solutions that won’t break the bank.
Environmental Impact
Plastic extrusions often get a bad rap when it comes to environmental concerns. However, advancements in recycling and sustainable production methods are changing the narrative.
Many manufacturers now use recycled materials in their plastic extrusion processes. This reduces waste and lessens the demand for virgin resources. The result? A smaller carbon footprint over time.
Furthermore, plastic extrusions can contribute to energy efficiency in various applications. For instance, insulation profiles made from these materials enhance thermal performance, decreasing energy consumption.
It’s crucial to consider that not all plastics are created equal. Biodegradable options have emerged on the market as well. These innovative solutions aim to minimize long-term environmental impact while still delivering durability and function.
By choosing wisely, industries can leverage the benefits of plastic extrusions without compromising ecological integrity. It’s about finding balance—benefiting both business needs and our planet’s health.
Applications of Plastic Extrusions
Plastic extrusions find their way into various industries, showcasing incredible versatility. From construction to automotive, their applications are vast and impactful.
In the building sector, plastic extrusions create window frames and siding that enhance both aesthetics and functionality. They provide energy efficiency while resisting harsh weather conditions.
The automotive industry benefits from lightweight plastic profiles used in interior trim and exterior components. These parts not only reduce vehicle weight but also improve fuel economy.
Packaging is another significant area where plastic extrusions shine. Flexible films and rigid containers crafted through this process ensure products remain safe during transport.
Medical devices often incorporate custom-extruded plastics for tubes or casings, adhering to stringent safety standards. Their ability to be molded into precise shapes makes them ideal for specialized equipment.
From signage to furniture design, the potential uses of plastic extrusions continue expanding across sectors. The adaptability they offer keeps innovation alive in countless fields.
Conclusion
When seeking long-lasting indicators, understanding the advantages of plastic extrusions can be key to making informed decisions. These versatile materials not only cater to a wide range of applications but also offer significant benefits in terms of durability and customization.
The ability to tailor designs ensures that businesses can meet specific requirements without sacrificing quality. Moreover, the longevity associated with plastic extrusions makes them an ideal choice for various industries.
From cost-effectiveness to positive environmental impact, the reasons for choosing plastic extrusions are compelling. As you explore options for long-lasting solutions, consider how these advantages can support your projects efficiently and sustainably.